关键词:火电厂:直流炉;汽包炉;给水处理;加氧处理; 氢氧化钠处理
20世纪80年代,直流锅炉氧化铁污堵、结垢速率高和锅炉压差上升速度快是中国火电厂发电机组较突出的问题之一。究其原因,主要是与给水系统铁含量高有关。因此抑制给水系统的腐蚀,降低给水铁含量是国内急需解决的问题。热工研究院通过实验室和工业模拟试验,确认了给水加氧处理是解决上述问题的有效方法。1988年我国开始在一台亚临界燃油直流锅炉机组上进行给水加氧处理的工业试验,取得了令人满意的结果,后来又分别在燃煤亚临界和超临界直流锅炉机组上均取得了成功的运行经验。目前世界很多国家在直流炉普遍应用给水加氧处理技术的基础上,正在大力研究和应用汽包炉给水加氧处理技术。
随着给水加氧处理技术在世界范围的普及,原来的给水联合处理cwt(combined water treatment)逐渐由更合理的名称——给水加氧处理ot(oxygenated treatment)所代替。我国在《直流锅炉给水加氧处理导则》行业标准中将已在电厂普遍采用的给水加氨、加氧处理称为给水加氧处理,简称ot[1]。但国内在同步研究和推广应用该项技术的过程中,仍碰到不少观念模糊和认识障碍方面的问题,如不能及时加以澄清和解决,将会影响国内给水加氧处理技术大面积的推广应用。
1 给水加氧处理的目的和适用范围
1.1 目的
给水处理采用加氧处理的目的就是通过改变给水处理方式,降低锅炉给水的含铁量和抑制炉前系统特别是锅炉省煤器入口管和高压加热器管的流动加速腐蚀(flow-accelerated corrosion,简称fac),达到降低锅炉水冷壁管氧化铁的沉积速率和延长锅炉化学清洗周期的目标。WWW.11665.COM
1.2 适用范围
给水加氧处理工艺的核心是氧在水质纯度很高的条件下对金属有钝化作用。为保证水质纯度(氢电导率小于0.1 μs/cm),要求系统必须配置凝结水精处理混床。采用加氧处理工艺的另一条件是低压加热器管材最好不是铜材,因为在氧化条件下铜氧化膜的溶解度较高,氧化铜腐蚀产物最终将转移到汽轮机高压缸沉积下来。但如果热力系统氧化铁腐蚀产物造成较为严重的结垢问题,即使低压加热器管是铜材,也可通过专项试验确定加氧处理水质的具体控制参数,在尽可能减小铜氧化物溶解的前提下,采用给水加氧处理,取得抑制铁氧化物的结果。
2 给水加氧的原理
2.1 全挥发处理(avt)方式下氧化膜的特点
根据氧化膜生成机理,电厂水汽循环系统的腐蚀又可分为电化学反应和化学反应。水与碳钢反应生成氧化膜的机理依据温度条件有所不同,从常温到300℃左右的范围内,水与碳钢通过电化学反应生成氧化膜。在400℃以上,蒸汽与碳钢通过化学反应生成氧化膜。
由于在低温条件下水作为氧化剂没有能量使fe2+氧化为fe3+并随后转化为具有保护作用的氧化膜覆盖层,氧化膜处于活性状态[2]。四氧化三铁的溶解度约在150℃时最大。提高溶液的ph值有利于降低氢氧化亚铁的溶解度。
在凝结水系统、低压加热器和第1级高压加热器入口的水温和化学介质条件下,当局部水流动条件恶化时,铁的溶解会转变为侵蚀性腐蚀,即会发生流动加速腐蚀(fac)(见图1)。
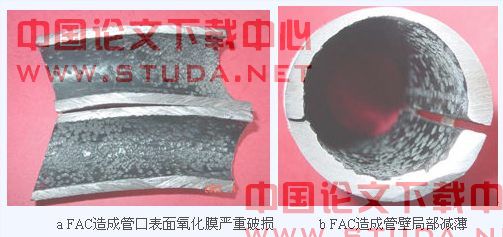
图1 某电厂高压加热器管入口发生的流动加速腐蚀
在300~400 ℃高温区,水分子具有能量使二价铁氧化为三价铁,因此在省煤器的出口段到水冷壁的金属表面形成了内层薄而致密、外层也较为致密的四氧化三铁氧化膜。此温度区应是化学反应与电化学反应混合区或过渡区。随着温度的升高,氧化膜生成的反应控制过程逐渐由电化学反应转向以化学反应为主。
通过上述关于无氧条件下形成氧化膜的特点讨论可看出,除高温段外,中、低温段的金属氧化膜是不够致密的,其四氧化三铁的溶解度较高,即使热力系统的水质接近理论纯度,或通过提高ph值尽量降低氢氧化亚铁的溶解度,但因在使用联氨处理的条件下形成的双层fe3o4氧化膜,由致密的内伸fe3o4层和多孔、疏松的fe3o4外延层构成,由于疏松的fe3o4外延层不耐水流的冲击,给水系统的局部会发生流动加速腐蚀,同时给水系统氧化膜释放出的微量铁离子仍会造成给水含铁量高及使下游热力设备发生氧化铁的污堵和沉积问题。
由于铁氧化物不断在热负荷高的部位沉积,在水流作用下生成了表面粗糙的波纹状垢层,该类垢层除降低锅炉受热面的传热效率外,还增加了流体阻力,造成锅炉压差不断上升。
2.2 给水氧化处理的原理
在给水加氧方式下,由于不断向金属表面均匀地供氧,使金属表面形成了致密稳定的“双层保护膜”。这是因为在流动的高纯水中添加适量氧,可提高碳钢的自然腐蚀电位数百毫伏,使金属表面发生极化或使金属的电位达到钝化电位,在金属表面生成致密而稳定的保护性氧化膜。直流炉应用给水加氧处理技术,在金属表面形成了致密光滑的氧化膜,不但很好地解决了炉前系统存在的水流加速腐蚀问题,还消除了水冷壁管内表面波纹状氧化膜造成的锅炉压差上升的缺陷。
3 给水加氧处理的条件
加氧处理必须在水质很纯的条件下才能进行。直流炉给水加氧处理时,只需考虑给水含氧量和给水含铁量的关系,严格控制给水的电导率即可。但汽包炉给水加氧处理除控制给水的电导率、含氧量和含铁量外,还要考虑炉水的电导率、含氧量。因此,汽包炉给水加氧处理的控制要比直流炉的复杂和困难些。由于汽包炉汽包对盐类的浓缩作用,除研究炉水水质的控制条件外,还要研究进一步改善凝结水精处理的运行条件,提高凝结水精处理的出水水质。
3.1 凝结水精处理出水水质
锅炉应用给水加氧的前提是机组配置有全流量凝结水精处理设备。凝结水精处理设备的运行条件和出水品质的好坏,是锅炉给水加氧处理是否能正常进行的重要前提条件,
直流炉要求给水的氢电导要小于0.15 μs/cm,凝结水精处理必须保证出水的氢电导小于0.10 μs/cm。汽包炉要求给水的氢电导要小于0.10 μs/cm,因而凝结水精处理必须保证出水的氢电导小于0.075 μs/cm。
3.2 取样监控
从以往的经验得知,尽管有些汽包锅炉从连续排污管引出的炉水的铁含量很小,但锅炉的结垢速率很高,与实际情况不符。说明以前炉水取样点主要是为监测炉水含盐量而设计的。亚临界锅炉的汽包结构与中、高压锅炉不同,给水分配管布置在汽包的底部紧靠下降管的入口。给水中的氧进入汽包后大部分自然要向汽包空间逸出,剩余部分混入锅水通过下降管进入受热面。锅水经加热和汽水分离装置后脱氧,因此无氧的锅水在循环过程中不断地将给水未来得及析出氧稀释后带入水冷壁。为防止水冷壁氧腐蚀,进入水冷壁的氧含量必须受到监测和控制。因此,应监测水冷壁入口的水质,即锅炉下降管的水质。
3. 3 加氧控制系统
氧化剂采用气态氧,由高压氧气瓶提供的氧气经减压阀针形流量调节阀加入系统。加氧点为2处:一处为凝结水精处理出口母管;另一处为除氧器出口母管。系统中选用精密的逆止阀防止发生给水倒流。加氧控制方式采用手动调节和自动调节并联控制。与直流炉给水加氧不同的是汽包炉给水加氧要求加氧量调节自动控制。一般以除氧器下降管加氧点为自动控制点,此法的优点是除氧器的排汽门开度不用严格控制。自动控制参数由给水流量、下降管氧含量和省煤器入口氧含量共同决定。
3. 4 锅炉结垢量
应用给水加氧处理前锅炉原则上应进行化学清洗,除去热力系统(省煤器、水冷壁和高压加热器及给水管线)中的腐蚀产物。这是由于以下原因:(1)给水加氧处理工艺没有“除垢”的作用,只是在原来的四氧化三铁氧化膜上通过部分四氧化三铁转换为三氧化二铁,形成了双层保护膜,双层氧化膜的厚度变化不大。(2)水冷壁管的氧化膜表面的波纹状垢在加氧后消失,可能与组成表面波纹状垢的大颗粒四氧化三铁被转化为细小的颗粒或被剥离有关。但水冷壁管的氧化铁垢层的厚度并没有明显减薄。(3)原先热力系统金属表面沉积的黑色四氧化三铁粉会转换为棕红色的α-fe3o4,仍覆盖在热力系统金属的表面,同时易造成在高温区氧气对金属仍有钝化作用的误解。(4)如果没有去除沉积在热力系统中的铜氧化物,在加氧处理开始后,铜的腐蚀产物会转到汽轮机高压缸沉积。
因此,对热力系统预先进行化学清洗非常必要,化学清洗除去了热力系统中铜铁腐蚀产物,在此基础上应用给水加氧处理,可在炉前系统获得最薄的保护性氧化膜,在水冷壁保持较低的氧化铁沉积速率。如因机组应用给水加氧处理时暂时没有条件进行化学清洗,则在即使成功应用了给水加氧处理工艺之后,也有必要尽早安排锅炉的化学清洗。
3. 5热力系统材质
3.5.1 司太立合金(钨铬钴合金)
国外在开发给水加氧处理技术的历史上,在使用过氧化氢做氧化剂时,曾发生过司太立合金的侵蚀问题。1979年德国报道了使用过氧化氢所发生的在水相此种材料的侵蚀(erosion)问题,损坏部位在给水泵阀及减温水阀上,经研究发现,这与司太立合金构件的结构有关,经改进结构或选用氧气做氧化剂,该问题得到彻底解决。
3.5.2 含铜量小于1%的铁基合金
国内外机组中有许多用该材料制成管系,如给水管道和锅炉连箱等。元宝山电厂#1机给水管路、汽水分离器(汽包)、循环泵入口过滤器及省煤器、水冷壁、过热器的部分联箱等部位的材质为15nicumonb5(材质含铜量为0.5~0.8%);大部分阀门的阀芯、阀座为斯太立合金。#1机组锅炉给水加氧处理的运行实践证明给水加氧处理不会造成这些管道的腐蚀。
3.5.3 铜合金
对于低压加热器管材为铜合金的机组能否采用加氧处理工艺,国内外有不同的意见。原因是铜合金在还原性介质中表面生成的是氧化亚铜(cu2o)保护膜,该膜有较低的溶解度。而在氧化条件下,氧化亚铜会转变为氧化铜(cuo),氧化铜的溶解度较高,铜离子会通过蒸汽的机械携带或溶解携带(蒸汽压力大于16.5 mpa)转移到汽轮机高压缸沉积,引起蒸汽通流面积减小,较低高压缸效率。
因此国外不赞同在有铜系统的机组应用给水加氧处理工艺。前苏联为在超临界机组应用给水加氧处理工艺,将低压加热器铜管换为钢管。
我国直流炉给水加氧处理的工业试验是在望亭有铜机组上进行的,试验证实给水的铜含量在加氧后有增加的现象,但通过调整给水的ph值,可将给水铜含量降低到小于3 μg/l。后来,广东黄埔发电厂、江苏常熟发电厂国产300 mw有铜机组(16.7 mpa)先后采用了给水加氧处理工艺,有效解决了省煤器和水冷壁氧化铁沉积速率高的问题。黄埔发电厂机组大修时检查高压缸并没有明显的铜沉积现象,常熟电厂因为汽轮机还未开缸检修,铜沉积的问题目前不清楚,但也还未发现汽轮机效率有任何降低的现象。
因此,了解了铜氧化物在不同条件下的特点,采取适当的措施,有铜机组也可采用给水加氧处理工艺,但应在尽量降低给水铜含量的同时,仔细监测在高压缸的铜沉积问题。
4 汽包炉给水加氧处理
我国大部分机组配备的是汽包炉,能否将加氧技术应用到汽包炉上,已成为国内倍受关注的问题。因为有些亚临界汽包炉的给水尽管采用了avt处理,但在该方式下其给水含铁量仍较高,已造成锅炉结垢率较高和高压加热器等设备结垢等问题。对这个问题急需有好的解决措施。根据直流炉加氧处理的经验,给水加氧处理是最有效的降低给水含铁量的方法。汽包炉给水加氧处理时,水中的溶解氧主要是对给水系统和疏水系统进行保护,而对锅炉本体的保护作用有限。关键要控制炉水水质,并避免炉水中有害阴离子在氧存在的条件下对锅炉本体产生的不良影响。
4.1 氢电导率控制
汽包炉给水采用加氧处理的前提是水质的高纯度。为满足这一要求,凝结水必须经过精除盐处理。凝结水精处理混床出水的水质指标比直流炉严格,必须保证出水的氢电导小于0.075 μs/cm.。
炉水的氢电导率是炉水中所有阴离子含量的综合指标,在无法监测氯离子的情况下,一般要求控制炉水氢电导率。如要控制炉水中的氯离子不超过100 μg/l,则炉水的氢电导率应控制小于1.2 μs/cm,正常运行时的期望控制值应小于1.0 μs/cm。
4.2 炉水ph值控制
试验证明,提高ph值可提高产生孔蚀的临界氯离子浓度。如用加氨的方法将ph值提高到8.5,170 ℃时可将氯离子临界浓度从0.04 mg/l提高到0.05 mg/l以上。如用加naoh的方法将ph值提高到8.5,这一温度下的氯离子临界浓度将会提高到0.35 mg/l以上。
在温度为350℃、时间为24 h的高压釜正交试验中,无氧(o2≤5 μg/l)、0.1 mg /l氯离子的条件下, 加naoh将ph值提高到9.5,膜的耐蚀性比平均水平高52.3%,即使将氯离子浓度提高到0.3 mg /l,也没有影响膜的耐蚀性。英国的经验已证明, 只要oh~浓度大于cl~浓度的1.5倍,就能抑制氯离子的破坏作用。因此,氢氧根对维持氧化膜的完整性及修复膜的缺陷有积极作用。
一定浓度的氯离子可以破坏氧化膜,造成炉管腐蚀损坏,naoh可使氯离子在有氧的条件下触发腐蚀的临界浓度提高到毫克每升级水平,因此确认调节和维持炉水ph值的最佳碱化剂是naoh。naoh用作炉水碱化剂曾受到条件的限制,naoh在炉管受热面多孔沉积物下或高热负荷区出现膜态沸腾时会浓缩到百分浓度,造成炉管的碱性腐蚀和苛性脆化。炉管产生naoh碱脆的条件有3个:高热负荷、高浓度naoh(>5%)和拉伸应力。在历史上的确在铆接锅炉和炉水含盐量较高的锅炉发生过此类损坏。另外,过高的碱含量也会造成锅炉损坏,例如某厂200 mw机组由于补给水钠含量较高,带入锅炉后炉水的氢氧化钠浓缩至8~14 mg/l,造成水冷壁管发生爆管事故。但随着锅炉制造技术和给水纯度的提高,引起炉管的碱性腐蚀和苛性脆化的条件已被消除。亚临界锅炉在设计上已充分考虑了避免产生膜态沸腾的措施,如受高热负荷的炉管采用内螺纹管,提高了防膜态沸腾的裕量。因此使炉水采用氢氧化钠处理成为可能。
在汽包炉水冷壁产生蒸汽处,随着热负荷的升高,氯离子会浓缩而降低金属的电位,同时,金属表面大量的汽泡对氧化膜的冲击作用及氧化膜本身产生的内应力都是破坏氧化膜的潜在因素,在这种环境中,只有氢氧根具有使金属的电位随热负荷的升高而明显升高的特点,可使水冷壁高热负荷区的金属表面保持钝化状态[4]。
在炉管产生蒸汽的高热负荷区,适量的naoh除可避免强烈沸腾的近壁层因潜在酸性杂质的浓缩外,还能避免此处生成沉积物,这是由于存在游离naoh,磁铁颗粒表面的正电荷使磁铁颗粒间互相排斥,在局部沉积的概率较低[5]。因而磁性氧化铁颗粒只有沉积在汽包或下联箱的底部。
naoh的作用原理可用金属钝化的吸附理论解释[5]。在稀溶液中,电位的梯度将使靠近阳极表面的水分子定向,因为此时水分子氧的部分将靠近金属,从金属上下来的阳离子不是进入溶液,而是定居在氧离子之间,而水分子中的氢离子则代替它进入溶液。若溶液中含有一定浓度的带负电荷的阴离子,同样的电位梯度将使它们把不带静电荷的水分子从金属表面置换下来。如果阴离子是oh~,氢氧根的氧的部分和金属氧化膜最外侧的原子因化学吸附而结合,一方面使金属表面的化学结合力饱和,从而改变了金属/溶液界面的结构,大大提高了阳极反应的活化能,使金属同腐蚀介质的化学反应能力显著减小;另一方面,由于氢氧根在吸附过程中排挤原来吸附在金属表面的水分子层,也就降低了金属的离子化过程。在金属表面已形成四氧化三铁氧化膜的条件下,氢氧根与二价铁和三价铁还会形成羟基铁氧化物,覆盖在金属表面,形成致密的保护膜。因此,氢氧根的吸附作用使金属保持钝化状态。在溶液中保持足够量的oh-,可阻止氯离子对氧化膜的破坏作用。
对于配有凝结水精处理的机组,炉水中的氯离子一般不超过200 μg/l,炉水中0.5 ~1 mg/l左右的naoh就足以抑制氯离子的破坏作用。应注意控制炉水ph值不大于9.4,以防范naoh在锅炉高热负荷区强烈沸腾的近壁层潜在的浓缩趋势。
4.3 炉水中含氧量的作用
氧化膜的完整性与氯离子的浓度、氧的浓度和氢氧根的浓度有关。在锅炉的高温区,过去常见的腐蚀损坏形式有沉积物下腐蚀、氢脆爆管等。这些现象都与给水带入的有害杂质有关。汽包炉高热负荷区氧化膜主要遭受炉水中的阴离子如氯离子的破坏,如氯离子达到了破坏氧化膜的某一临界浓度,则有氧存在的情况下会加剧氯离子的破坏程度。英国实验室的动态试验提出了氧浓度和氯离子浓度乘积的关系式[6],表明氧和氯离子浓度联合作用时触发金属腐蚀的临界值:
〔o2〕×〔nacl〕= 0.4 (mg/l)2
即在300~360 ℃条件下,炉水中的含氧量和nacl含量的乘积不超过0.4时,锅炉金属在短时间内不会发生腐蚀。而naoh可使这一临界值达到20(mg/l)2。
汽包炉给水加氧处理工业试验结果表明:在用氢氧化钠调节炉水ph值,控制氯离子不超过100 μg/l的条件下,炉水中的氧含量控制小于15 μg/l是安全的;另一方面,在锅炉水冷壁高热负荷区,由于汽液两相分配系数的关系,炉水中氧全部进入汽相,进入炉水中的微量氧不会引起锅炉金属的腐蚀。
4.4 给水含氧量和下降管炉水含氧量的关系
在控制炉水盐类浓缩的同时,应使进入水冷壁的氧尽量小。一般在炉水氢电导率小于1.5 μs/cm的条件下,下降管炉水氧含量应小于10 μg/l;炉水氢电导率小于1.0 μs/cm条件下,下降管炉水氧含量应小于15 μg/l,具体规定多少,应根据炉水含盐量情况确定。给水溶解氧和下降管溶解氧与机组负荷间的关系需通过试验确定。
4.5 汽水品质控制指标
锅炉给水采用加氧处理的汽水品质按表1推荐值执行,未列入的其余控制指标按原有标准控制。
表1 汽包炉给水加氧处理汽水品质控制指标
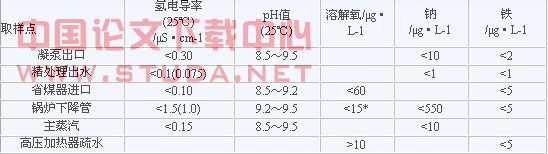
注:(1)氢电导率栏括号内数值表示期望控制值;
(2)*表示下降管氧含量具体应根据炉水水质、炉水循环方式和试验来确定。
5 对疏水系统的影响
在给水全挥发处理(avt)条件下,加热器疏水系统的管材和壳体的汽液分界区在运行中可能发生水流加速腐蚀,在停备用期间易受氧腐蚀。高压加热器的腐蚀产物随疏水进入除氧器,特别是机组启动时,大量的锈蚀产物会进入热力系统,沉积在锅炉受热面。
给水处理采用加氧处理,可使加热器疏水系统的水相金属表面生成保护性氧化膜,有效地抑制水流加速腐蚀和停备用腐蚀。直流炉采用给水加氧处理的氧含量控制范围(30~150 μg/l)在关小加热器排汽门的前提下,可满足疏水中氧含量大于30 μg/l的要求。但在汽包炉,由于给水氧含量一般控制在10~60 μg/l,由蒸汽带入的氧含量很小,即使在加热器排汽门关小的情况下,也很难满足疏水系统的氧含量要求。因此,为确保疏水系统得到保护,必须尽量提高疏水的氧含量,必须在运行时完全关闭排汽门。
为防止停运期间的氧腐蚀,在机组停机和启动期间又需要打开排汽门,一方面防止停运期间的氧腐蚀;另一方面确保机组启动阶段排出二氧化碳等不凝性气体。如运行期间加热器的排汽门关不严,氧含量达不到10~20 μg/l,则应考虑调整给水ph值,以保证蒸汽ph值可满足疏水系统防腐蚀的需要。
6 对蒸汽系统的影响
对国外所进行的调研结果表明:加氧处理工艺问世近30年来,全世界85%的直流炉和5%以上汽包炉已成功应用了给水加氧处理工艺。至今还没有关于采用给水加氧处理会明显引起热力系统高温段金属表面氧化皮增厚或脱落问题的报道。目前最新发展的超超临界机组的给水处理工艺唯有采用加氧处理这一结论也已得到举世公认。如此长时期的工业实践和大面积的推广应用的事实本身就是加氧处理技术成熟性的最好证明。
我国在研究应用给水加氧处理技术的实践中,曾遇到有的机组因怀疑主汽门的卡涩与加入的氧气有关而中断采用给水加氧处理工艺的情况。经调研,主汽门卡涩问题在国内较普遍,氧化皮问题在所调查的电厂中也有不同程度的影响。从采用和未采用给水加氧处理的电厂的对比结果看,给水处理的方式与主汽门卡涩没有直接的关联。据有关电厂介绍,加强监测和缩短检修周期,并彻底除去主汽门本体的氧化皮,是目前控制主汽门卡涩的较有效的办法。从治本的角度,应选用抗氧化和抗脱落性能更好的材料。
给水加氧处理对高温段金属氧化的影响到底有多大,可根据氧气和水蒸汽分压来判断。假设1 kg水蒸汽的分压为1 pa,由给水加氧处理所带入蒸汽中的氧气一般小于150 μg/l,氧气与水蒸汽的分压比为10-7~10-8 pa,与高温水蒸汽的氧化作用相比,如此微量的氧气的氧化作用微乎其微。美国epri在机组蒸汽系统高温氧化方面的研究结果[3]明确了高温氧化皮问题与温度和材质有关,与水工况无关(包括给水加氧处理工况)。
7 给水加氧处理是否会引起氧腐蚀问题
加氧处理之所以可使炉前系统金属的表面产生钝化,除水质高纯度这一先决条件外,还必须有水流动的条件,即在流动的高纯水中加入氧气才能在金属表面产生保护性氧化膜。
氧腐蚀发生的一般原理是在不流动的水中溶解氧在局部发生了浓度差,浓差电池引起金属氧化膜局部破坏,形成点状腐蚀。过去水处理工艺较落后时,运行中的锅炉水冷壁如有大量盐类沉积物,水中的溶解氧会加速沉积物下的腐蚀。现在,在电厂机组热力系统发生的氧腐蚀一般都与停机时系统内不能充分干燥有关。暴露在空气中的金属表面有湿分时,氧腐蚀立即发生。因此,机组停运时,及时隔绝空气或保持热力设备干燥是停备用保养是否有效的关键。
在采用给水加氧的条件下,原则上经化学清洗的锅炉受热面没有盐类沉积物或大量的氧化铁沉积物。直流炉蒸汽中氧含量在50~150 μg/l,汽包炉蒸汽中氧含量在10~50 μg/l。采用加氧处理的机组,在启动时首先采用无氧工况运行,待水质条件达到加氧处理的要求后方可开始加氧。在加氧工况下,系统的氧化还原电位一般在+50~+300 mv之间,金属处于完全钝化状态,加氧前已存在点腐蚀不会进一步扩展。
8 给水加氧处理的效果评定
评定应用给水加氧处理技术所产生的效果,主要有氧化还原电位、给水铁含量、水冷壁结垢速率和锅炉压差等指标,还可用凝结水精处理混床的运行周期和运行成本等经济效益指标进行评定。
8.1 给水系统的氧化还原电位(orp)
氧化还原电位指标是表明热力系统处于氧化性介质还是还原性介质的一个重要参数。一般水汽系统的氧化还原电位在avt方式下约为-350 mv。停止加入联氨后,给水的氧化还原电位可达到-50~0 mv左右,加入氧气后给水的氧化还原电位应达到+50~+350 mv。
8.2 热力系统含铁量
给水处理采用加氧处理工艺后,热力系统运行中的铁含量大大降低,氧化铁腐蚀产物的粒径大大减小。尤其是给水系统的局部流动加速腐蚀得到了控制,保护性双层氧化膜使炉前系统的金属表面完全钝化。因此,给水系统的平均铁含量可从3~8 μg/l 降低到0.5~3 μg/l;疏水系统特别是高压加热器疏水的铁含量大大降低,疏水系统应得到完全保护。
8.3 锅炉的结垢速率
锅炉的结垢量由2部分构成,即自身腐蚀产物和给水带入的铁氧化物的沉积。机组投运后,水冷壁管的金属表面在一定的热负荷条件下会形成氧化膜,氧化膜的厚度与热负荷强度有关。热力系统的铁氧化物也会随给水源源不断地带入水冷壁受热面,在热负荷高的区域沉积下来,形成氧化铁垢,后者是结垢速率升高的主要因素。锅炉给水采用加氧处理,最大限度地降低了铁氧化物在受热面的沉积速率,使水冷壁的结垢速率降低。因此,加氧处理一般都可使铁氧化物在受热面的沉积速率降低80%以上。
用管段垢量来评定结垢速率,要求管段运行时间要长,才能得到准确结果。因为结垢和时间并非线性关系,开始阶段结垢较快,然后逐渐慢下来。因此用氧化铁沉积速率可更科学地评定其效果。
8.4 锅炉压差
给水处理采用ot方式运行后,由于省煤器和水冷壁金属表面形成了致密光滑和平整的垢层,直流炉的锅炉压差不再上升。
8.5 凝结水精处理混床的运行周期
在avt方式下凝结水精处理氢型混床在出水氢电导率小于0.1 μs/cm时的全流量运行周期一般为3~7天,因为avt方式下的加氨量较高,混床中的阳树脂很快失效。在给水加氧处理条件下,由于氨含量降低了5~10倍,阳树脂的运行周期大大提高,因而凝结水精处理混床的运行周期可延长3~5倍以上。因为与系统的加氨量有关,因此,汽包炉给水加氧处理后的凝结水精处理运行周期延长这一效益比直流炉小些。
8.6 经济效益指标
应用给水加氧处理获得的直接和间接的经济效益非常可观,大大降低了机组的运行成本,如应用给水加氧处理的机组提高了设备的安全性和可靠性,减少了因介质因素引起的非计划停机的几率。经济效益指标可计算部分主要指标有:(1)延长了锅炉的酸洗间隔所节约的化学清洗费用。(2)减少了机组的加药量费用。(3)延长凝结水精处理设备运行周期而节约的再生剂用量和自用水费用。(4)减少汽包炉锅炉连排和定排造成的热量损失折算成标准煤的费用。(5)减少除氧器排汽造成的热量损失折算成标准煤的费用。(6)降低直流炉锅炉压差节约的给水泵动力消耗费用。
参考文献:
[1] dl/t 805.1—2002,火电厂汽水化学导则 第一部分:直流锅炉给水加氧处理导则[s].
[2] vgb-r450le 1988,vgb guidelines for boiler feedwater, boiler water, steam of steam generators with a permissible operating pressure >68bar
[3] t h mccloskey, r b dooley, w p mcnaughton. turbine steam path damage: theory and practice[m].epri, 1999.
[4] п.a.阿科利津. 热能动力设备金属的腐蚀与保护[m].北京:水利电力出版社,1988.
[5] u r evans. 金属的腐蚀与氧化[m].北京:机械工业出版社, 1976.
[6] g m w mann, r gransey. waterside corrosion associated with two shift boiler operation on all volatile treatment chemistry[j].materials performance,1980,p32.
[7]火电厂蒸汽通流部件高温氧化皮的影响与防治对策研讨会论文集[c].中国电机工程学会火电分会,2002.