摘 要:壳管式油冷器广泛应用于电厂的各主要设备中, 新型高效油冷器的开发和研究是目前人们所关注的一个热点问题。文章分析了传统管壳式冷油器存在的问题, 指出同时强化管程和壳程的换热是开发新型高效油冷器的主要方法, 并给出了几种适用于冷油器的强化传热管型,以及应采用的壳程管间支撑形式。基于此,设计了一种将连续螺旋折流板与齿形翅片管搭配使用,两种传热强化措施结合起来的连续螺旋折流齿形翅片管冷油器。利用传热特性测试装置, 以油-水为工质, 对其进行试验研究, 得到了油冷器的传热与阻力性能曲线。实验结果表明: 该种油冷器的壳程油侧换热系数可达1200~1400w/(m2·k), 而压降比同等条件下的弓形折流板光滑管油冷器降低25%~45%,这为电厂冷油器的改造提供了一种新的选择。
关键词: 连续螺旋折流板; 弓形折流板; 齿形翅片管; 强化传热; 冷油器
水冷壳管式冷油器是电厂中应用量大且面广的一种附机设备,如汽轮机的主冷油器、给水泵和风机冷油器、磨煤机冷油器等,其传热效率的高低和抗腐蚀泄漏性成为影响电厂中相关设备正常运行的关键。目前,电厂所用的壳管式冷油器大都仍采用铜光滑管作为传热管型,弓形隔板作为管间支撑形式。该类冷油器存在二方面不足:一是腐蚀和泄漏问题突出;二是当壳程油侧压降在0.1mpa左右时,总传热系数一般不超过700w/(m2·k)[1]。因而其传热效率很低,导致冷油器无法将油温冷却到给定值,使得相关的设备出现故障1。
强化冷油器换热效率的主要方法有两种:一种是将冷油器的基本换热元件——传热管,由光滑管改为强化传热管,以减薄流体在管壁处的层流边界层,降低热阻;另一种是采用低流阻壳程管间支撑物,通过消除流体流动和传热过程中的死区,变壳程流体横向冲刷流为纵向螺旋流,提高壳程流体的流速。wwW.11665.coM基于这一强化传热思路,在分析传统管壳式冷油器存在的问题,及如何解决的基础上,本文设计了一种将连续螺旋折流板与齿形翅片管搭配使用,两种传热强化措施结合起来的连续螺旋折流齿形翅片管冷油器。以油-水为工质,利用传热与流阻特性试验装置,对其进行试验研究,得到了油冷器的传热与阻力性能曲线。可为这种换热器的工业应用及与其他强化传热管的结合使用提供参考。
1 冷油器存在的主要问题
1.1 管板的泄漏
现有的壳管式冷油器换热管为铜管,而管板和壳体、水室等均为碳钢材料。换热管采用胀接工艺与管板相连接,胀接过程中会在管板上尤其是在连接部位生成较大的残余应力。这部分应力在一定工况下将释放出来,导致胀口开裂。另一方面,由于管板和换热管材质不同,膨胀系数相差较大,在冷油器工作时由于温度变化、振动和频繁的起停影响,使冷油器承受的热负荷和机械负荷经常处于交变状态,造成金属的疲劳,易产生胀口松动,导致冷却油泄露。
以铜管为换热管,碳钢材料为管板、壳体和水室的冷油器也具备构成原电池的条件,易发生电化学腐蚀,使管板等表面出现腐蚀凹坑[2]。长期地电化学腐蚀,加上应力腐蚀的共同作用,最先在胀口处开始出现泄漏。
1.2 换热管腐蚀与振动引起的泄漏
腐蚀与振动是引起冷油器内的铜质换热管泄漏的2个关键因素。冷却水的侵蚀性、流速较高且紊乱,加上冷油器本身苛刻的运行工况,使冷油器的腐蚀问题异常突出。诱发冷油器内铜管泄漏的腐蚀主要是局部腐蚀,它包括的脱锌腐蚀(层状脱锌和塞状脱锌)、微生物腐蚀、应力腐蚀和冲击腐蚀。腐蚀由管内壁向外发展,最深处可穿透至外壁。当腐蚀区域丧失应有的机械强度时,便会在很小的应力作用下,在腐蚀区域产生贯通性裂纹,发生腐蚀失效,造成冷油器铜管泄漏。
传统的冷油器采用弓形隔板作为管间支撑形式,这种结构会使壳侧油产生横向冲刷流。当冷却油横向掠过换热管时会形成旋涡,然后再与管子分离。旋涡的产生和分离呈现周期性变化,导致换热管产生振动。另外,弓形隔板冷油器的壳程油流体也会发生弹性激振、紊流抖振等,同样会导致换热管束振动。当达到共振点时,振幅较大,导致相邻管子、管了与弓形隔板之间发生相互碰撞或管子撞击壳体。振动碰撞过程中,管壁发生菱形磨损,逐渐变薄直至泄漏。另外,振动还会在管了内部产生疲劳损伤和弯曲塑性变形,加上冷却水的腐蚀和侵蚀作用,使疲劳损伤加剧,造成管壁产生裂纹,管子破裂,严重时甚至折断而引发泄漏事故。
1.3 冷却效果差
传统的管壳式冷油器采用弓形折流板支撑管束,油流体在壳程呈“z”字形流动,在转折区及进出口两端涡流的滞留区均会形成流动和传热的死区(见图1),减少了有效传热面积,并在死区内形成传热垢层,大大降低了传热效率。另外,弓形折流板也使油流体垂直冲击壳体壁面,造成较大的沿程压降。因此,这种结构的冷油器总传热系数k值一直停滞在较低状态。
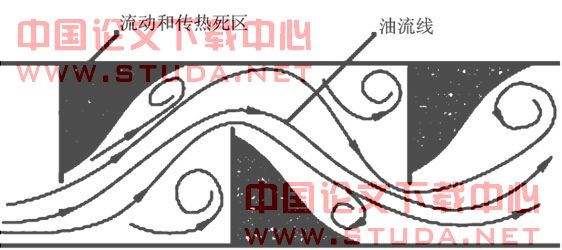
图1 弓形折流板冷油器壳程流场示意图
冷油器管束由光滑管组成时,无强化换热效果。在管内冷却水侧,由于水中泥沙等机械杂质较多,随着冷油器运行时间增长,会逐渐沉积在换热管内壁上,严重时堵塞部分冷却水管。这些沉积在换热管内壁表面上的污垢一方面会增加冷却水管的导热热阻,使冷却效果变差;另一方面也使流道横截面的减少甚至堵塞,降低冷却水流量,致使冷却效果大幅度下降。
2 强化传热的二大途径
2.1 强化管程换热
以一种最简单的管壳式换热器为例,其总传热系数k可表示成:
(1)
式中:a0/ai为换热管外表面积与内表面积之比,λ为管子导热系数,δ为管子壁厚。冷油器的管壁很薄,导热系数很大,λ/δ可以忽略。由(1)式可知欲增加k,就必须增加管子内、外侧流体换热系数hi和h0。但当hi和h0相差较大时,增加它们之中较小的一个最有效。
冷油器的管束由光滑管组成时,管外油侧换热系数h0约在96.5~159.6kw/(m3·k),而管内水侧换热系数hi可达1500kw/(m3·k)以上。显然冷油器热阻主要在油侧,占总热阻的70%~80%。因此,采用强化传热管来有提管外换热系数h0以减少壳程油侧热阻,是开发高效能冷油器的技术关键之一。
按照bergles的分类[3],对流换热的强化技术可分为无源强化技术(passive technology)、有源强化技术(active technology)和复合强化compound enhancement)。被动强化技术除传热介质的输送外无需外加动力,而主动强化技术则需要外加能量以强化换热过程。冷油器管束的强化适合采用无源强化技术,它包括有[4]处理表面、粗糙表面、扩展表面等7种,具体方法见表1。
表1 对流换热强化技术的分类与实现方法
理论研究表明,对于冷油器这类高粘性、低流速换热器,无源强化传热应采用彼此间断的高肋片传热管。但该类管型大都只能采用铜材质,如花瓣管必须采用铜材制造,不仅设备成本高,应用也受到限制。为此,笔者开发出一种带有周向三维翅片的齿形翅片管(见图2),可采用钢材质管制造。
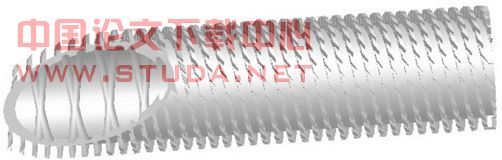
图2 钢质齿形翅片管外观
齿形翅片管具有间断性的三维翅片结构,当用于冷油器这类单相对流换热时,间断性翅片可周期性割断翅片上油流体的滞留层,并使油的流向不断改变和边界层剥离,强烈地降低滞流层的厚度和热阻。同时,沿轴向螺旋状连续分布的齿形翅片避免了管流的周向旋流,前后邻接、间断性的齿形翅片迎流面抑制了翅片下游死区及涡列形成,降低了形体阻力及其导致的能耗,这对降低热阻、提高换热系数非常有利。
2.2 强化壳程换热
通常,三维翅片管在增大传热系数的同时,会增加壳程油的流动阻力,因此必须采用合理的支承结构,以减小流动阻力。近年来,人们研究开发出了各种不同形式的管间支撑物,以强化壳程的换热过程。壳程管间支撑物主要包括杆式(折流杆)、环式(空心环)、板式(单弓形、多弓形、螺旋形、整圆形)和换热管自支承等形式。其中,最早由lutcha j.和nemcansky j.[5]于1983年提出的螺旋折流板就是一种流阻性能优良的支承结构,它使壳程流体作螺旋运动以强化换热器壳程的传热。和传统弓形折流板换热器相比,具有以下几方面的优点[6]:(1)壳程流体呈螺旋状柱塞流动,不存在流动死区,适宜于处理含固体颗粒、粉尘、泥沙等流体;(2)壳程压力损失小,单位压降下壳程传热系数高,减少了动力消耗;(3)能有效抑制壳程流体的污垢累积沉淀,提高换热器有效使用周期。对于冷却油这类高黏度流体而言,其换热效果更加突出,图3[7]是一种螺旋折流板换热器结构。
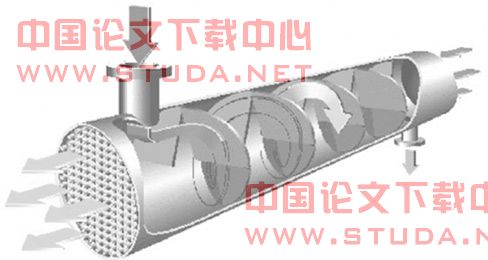
图3 螺旋折流板换热器结构示意图
螺旋折流板换热器分为连续型(continuous baffle)和搭接型(sector baffle)两种,其中搭接型又分为连续搭接型(continuous sector baffle)和交错搭接型(staggered sector baffle)。目前所使用的螺旋折流板大都由两块或四块扇形铜材质平板搭接而成,两块相邻折流板间形成一系列三角形空间,容易使沿折流板流动的介质形成短路漏流,减少理想通道的流量;也使得壳侧流动偏离真正的螺旋流动[8],削弱了换热效率。同时安装、运输及使用场合都受到较大限制,为此文中采用了钢质连续螺旋折流板(见图4)。以便能够使冷油器壳侧油的流动实现真正的螺旋流动,减低壳侧的压降,提高换热效率,同时缓解冷油器的振动问题。
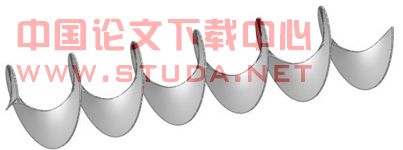
图4 连续螺旋折流板结构图
3 实验系统
为使所设计的连续螺旋折流板齿形翅片管冷油器应用于电厂,本文通过实验研究方法对其在水油为换热工质的系统上进行动态特性试验。
3.1 实验装置与流程
油冷器性能实验系统如图5所示,主要包括油路循环系统、水路循环系统以及流量、温度、压差测量系统,可实现油水换热的实验功能。
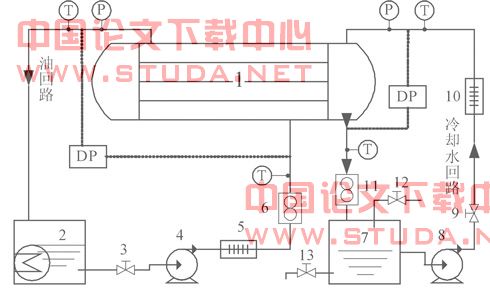
1-冷油器; 2-电热油罐; 3,9-阀门; 4-油泵; 5,10-快速加热器
6,11-流量计; 7-冷水箱; 8-冷水泵; 12-补水阀; 13-排污阀
t-热电偶; p-压力计; dp-差压计
图5 冷油器换热实验流程图
采用32号润滑油-水作为工作介质,其中油走壳程,为热流体;水走管程,为冷流体。先将润滑油加热到预定温度,然后由油泵引出至快速加热器,通过涡轮流量计送入油冷器壳程冷却,再返回油箱构成循环。来自水箱的冷却水由水泵引出,经过快速加热器送入油冷器的管程,与管外油换热后经涡轮流量计流回水箱。
本次实验主要测量3个物理量,即流量、温度和压差。润滑油和水的流量由变频油泵及水泵控制,通过lwz-32型涡轮流量计测量,其测量精度为±2.5%。油冷器进出口油温和水温采用铜-康铜热电偶采集,通过温度传感器由计算机测量,量程为0~200℃,精度0.1℃。油压和水压用0.4级精密压力表测定,偏差小于5%。压差测量采用3501差压变送器,量程为0~62.2 kpa,精度为0.25%。
3.2 试验元件
为便于比较,冷油器采用浮头管板式结构,实验时只需更换不同的传热管束和管间支撑物就可以构成不同内部结构的换热器。本次实验元件包括:弓型折流板光管冷油器(简称冷油器1),连续螺旋折流板光管冷油器(简称冷油器2),连续螺旋折流板齿形翅片管冷油器(简称冷油器3)。本冷油器制造后,壳程、管程均以0.8mpa压力做水压试验,各种冷油器的几何参数及布置形式见表2。
表2 3种冷油器的布置形式
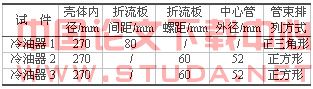
实验采用的齿形翅片管结构见图2,材质为碳钢,传热管坯管外径do为16mm,壁厚2.5mm,长l为2.4m,管间距pt为16mm。齿形翅片管是一种一体化的双侧强化传热管,由φ16×2.5无缝钢管在专用设备上经专门设计的模具和特殊工艺分三次成型加工而成,管子的内、外侧面具有不同的几何结构,结构参数见表3所列。
表3 实验管的几何结构参数
3.3 实验数据处理方法
本次实验主要测量流量、温度、压差3个物理量。实验中,将这3个物理量采集到计算机进行实时运算,判断热平衡。若平衡时吸热量和放热量相差在±10%内,认为实验数据可靠,予以采用。威尔逊热阻分离法要求的限定条件少,适合于管壳式冷油器的传热试验数据处理。本文应用热平衡法求出冷油器的总传热系数后,再运用威尔逊热阻分离法将壳侧换热系数分离出来。
利用冷油器进出口压降δp计算阻力系数,阻力系数ξ可由下式确定:
(2)
式中: δp为进出口压降,pa;ρ为润滑的密度,kg/m3;do为传热管坯管外径,m;de为壳程当量直径,m;l为传热管长度,m;u0为润滑壳程流速,m/s。
4 试验结果及分析
4.1 流动阻力特性
油冷器壳程总压降δp随着壳侧油流量ws的变化如图6所示,相应的壳程阻力系数与油流速的关系见图7。从图6和图7可见:相同壳侧油流量下,连续螺旋折流板式冷油器(冷油器2和冷油器3)的壳程阻力要小于弓型折流板式冷油器(冷油器1)。相同的壳侧流量下,冷油器3的壳程压降稍大于冷油器2的壳程压降。
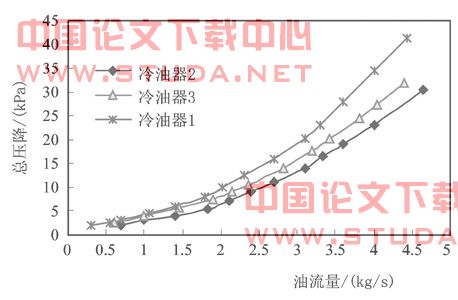
图6壳侧压降随油流量的变化
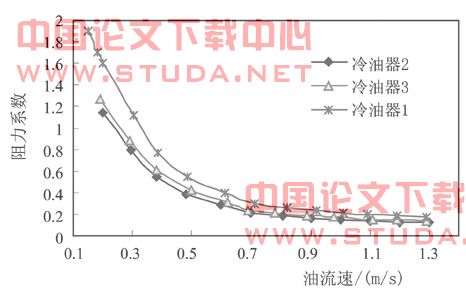
图7 阻力系数随油流速的变化曲线
油流速为0.15~1.3m/s时,油冷器3的壳程阻力系数为0.11~1.52。相同流速下,比相同管间支撑物的油冷器2高5%~15%,这是由于三维齿形翅片管增大了油的流动阻力。然而,要比弓形折流板油冷器1低25%~45%,这是由于连续螺旋折流板使得油流体呈纵向流动,可有效减小流动阻力,且流动阻力减小率大于齿形翅片管引起的流动阻力增长率。
4.2 传热特性
将实验结果以总传热系数k对壳程油侧压降δp作图(如图8所示),并以壳侧换热系数α0对壳侧壳侧油的流量ws作图(如图9所示),可比较出不同试件的传热性能。从图8和图9可见,相同壳侧油压降或流量下,冷油器1的壳侧总传热系数或换热系数小于冷油器2和冷油器3,压降或流量越大越明显。这是由于连续螺旋折流板冷油器不存在滞止死区,且油流体以较均匀流速沿螺旋通道包裹式的冲刷管束,有利于壳侧换热的提高。
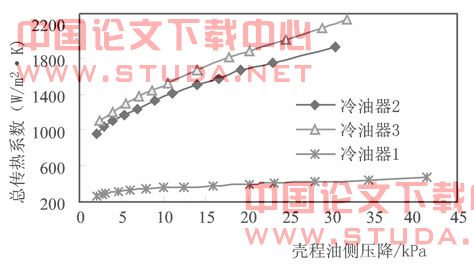
图8 总传热系数随油侧压降的变化
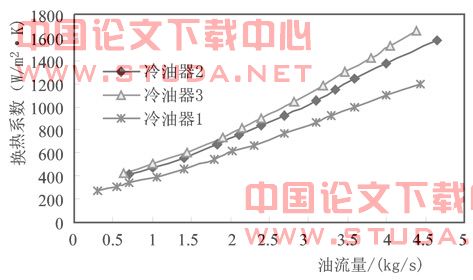
图9 换热系数随油流量的变化
由图9还可见,在主流速区,冷油器3的油侧换热系数达1200~1400w/(m2·k),稍大于相同工况下冷油器2的1050~1210w/(m2·k)。这是由于壳侧油流体在作轴向流动时,齿形翅片管的三维翅片使油顺利进入翅片根部,提高了根部油的置换速度,并进一步激发油产生扰动。另一方面,间断性的三维翅片对油流体有切割作用。两者共同作用的结果是破坏了热边界层,提高了换热系数。
4 在电厂冷油器中的应用分析
某火电厂4号机组的3台gl-60-ⅱ型冷油器自2002年开始频繁发生铜管泄漏,并逐年恶化,须实施改造。拟将原弓型折流板铜光管冷油器改为本文提出的连续螺旋折流钢质齿形翅片管冷油器。采用以上实验结果,依据该冷油器运行工况,得到改造前后的冷油器的传热性能计算结果如表4所列。从表4可看出,油冷器的传热与阻力性能均可达到设计要求,达到改造的目的。
表4 油冷器改造的主要参数对比
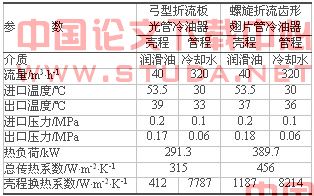
外,螺旋折流板齿形翅片管油冷器的总传热系数不仅较原冷油器高30%以上,且防垢性能也相当好,加上其优良的低流阻系数,可使冷油器功耗大大降低,为电厂带来可观的经济效益。
5 结 论
管板的泄漏、换热铜管腐蚀与振动引起的泄漏,以及冷却效果差是传统弓形折流板油冷器存在的主要问题。改变油冷器内部结构,采用间断性的三维翅片管强化管程换热,同时采用螺旋折流板作为管间支撑物以强化壳程换热是解决这一问题的关键。基于这一思路,本文提出了一种新型的高效油冷器——连续螺旋折流齿形翅片管冷油器。其壳程换热系数达1200~1400w/(m2·k),而壳程流动阻力较弓形折流板油冷器低25%~45%。具有较好的强化传热、低流阻和抗结垢性能,应用于电厂冷油器的改造可产生较好的高传热和低能耗效果,使油冷器长期高效稳定运行。
参数文献
[1] 张正国, 林培森, 王世平等. 水冷壳管式油冷却器传热强化实验[j]. 热能动力工程, 2000, 15(5):564, 566
[2] 张伟. 电站冷油器的运行分析与强化传热研究[j]. 山东电力技术, 2003, (5):7~9
[3] bergles a e. some perspectives on enhanced heat transfer second generation heat transfer technology[j]. asme journal of heat transfer,1988,110:1082~1096
[4] 夏再忠. 导热和对流换热过程的强化与优化[d]. 清华大学工学博士学位论文, 2001, pp.15~16
[5] lutcha j, nemcansky j. performance improvement of tubular heat exchangers by helical baffles[j]. trans icheme, part a, 1990, 68(5):263~270
[6] 王晨, 桑芝富. 单螺旋和双螺旋折流板换热器性能的研究[j]. 高校化学工程学报, 2007, 21(6):929~935
[7] m.r. jafari nasr, a. shafeghat. fluid flow analysis and extension of rapid design algorithm for helical baffle heat exchangers[j]. appl. therm. eng. (2007), doi:10.1016 /j.applthermaleng. 2007.10.021
[8] 王良, 罗来勤, 王秋旺等. 螺旋折流板换热器中阻流板对换热及沿程压降的影响[j]. 工程热物理学报, 2001, 22:173-176