摘要:
目前 光学塑料非球面零件在各种光电仪器中的 应用 越来越普遍。针对在注射成型光学塑料零件时对质量的特殊要求,本文介绍了利用注射成型cae(computer aidedengineering)软件moldflow,通过对塑料填充过程、保压过程和冷却过程的模拟 分析 ,对在成型中各工艺参数和模具结构 影响 光学塑料零件的残余应力和收缩率等最终质量 问题 进行了 研究 。从工艺参数的选取和模具结构设计等方面,提出了如何改善成型光学塑料零件质量的措施,给出了模具面形成型前补偿的 方法 。通过采用最大实体原则,利用moldflow分析结果进行模具面形补偿最优化 计算 。
关键词:注射成型;cae;光学塑料零件;最优化;面形补偿
一、引言
随着近代光学和光 电子 技术的飞速 发展 ,光电仪器以及构成这些光电仪器的零件发生了深刻而巨大的变化。由于模具材料、模具制造技术和精密模压工艺的发展,所以可以采用模压技术加工精密光学塑料零件,特别是非球面光学零件、透镜阵列和其它一些难以加工的特殊形状的零件。精密模压成型技术适于大批量生产,成本较低,它适宜制造各种复杂形状的光学零件[1]。虽然塑料光学零件耐热性差、线膨胀系数大、双折射大等,但它却具有制造成本低、易于制造复杂形状及非球面、重量轻、抗冲击性能好等优点。wWW.11665.CoM随着成型技术、新型塑料材料、镀膜技术的发展,光学塑料零件的应用越来越广泛。
目前,国外各种光学塑料零件加工工艺已经比较成熟,可以 经济 地加工高精度的光学塑料零件。相比之下,国内仍采用传统的工艺进行加工,加工的零件也以玻璃产品为主,光学塑料的制造和应用还比较少。由于计算机硬件及cae(computer aidedengineering)软件的发展,所以可以利用软件来提高光学塑料零件的成型质量并且缩短开发周期。
二、光学塑料零件注射成型的特点
工程塑料零件成型的精度一般在0 1~0 01mm级,而光学塑料零件成型的精度则在微米级,其面形精度在波长级,如在cd读写头中的塑料非球面透镜的形状精度要求在0 1μm以内。光学塑料成型的任何内部和外部缺陷都是不允许的,例如熔接线在普通的塑料成型中只是降低了此处的机械强度,而在光学塑料零件中,熔接线直接影响光学性能,象气孔等内部缺陷对工程塑料的应用影响并不大,而在光学塑料零件中,则是严重的缺陷。
热塑性塑料最常用的成型方法是注射成型法和注射压缩成型法。注射压缩成型法得到的产品面形精度最高,产品的面形几乎可以和模具的面形完全一样。但由于注射压缩成型设备比普通注塑机贵得多,在我国使用得还不广泛,大多数厂家只有普通的注塑机,所以如何用普通的注射成型法生产高精度的光学塑料零件有着很重要的现实意义。
三、cae在注射成型中的作用
目前,我国的注塑模具设计和注塑工艺的处理还主要依靠经验。模具加工出来后进行试模,如果产品不合格,再进行修模或改进注塑工艺,这样可能需要反复多次,不仅造成模具设计周期延长、模具费用和生产成本提高,更重要的是即使最有经验的设计人员也不可能把各种因素都非常准确地考虑进去,从而使模具设计质量不高,不能模塑出高质量的产品。利用cae技术可以设计出高质量的模具,给出最佳的工艺参数,减少试模和修模次数,这将大大缩短设计周期,降低成本。
简单地说,cae就是在计算机上对产品进行模拟分析,以此来代替试制和试验。塑料注射成型的cae主要是对塑料的流动状态、压力分布、冷却过程等进行模拟分析。cae能模拟塑料注塑零件的工艺条件,以获得最佳的模具结构和工艺参数,预测制品的几何尺寸、微观结构以及其最终性能。采用cae技术,可以使工程技术人员通过对塑料融料在型腔内的流动、保压及冷却进行全面的分析,以此来改进模具的浇注系统、冷却系统,调整成型工艺条件,可以预测填充的剪切应力、熔接线等,提高试模的一次成功率,提高产品质量和生产率。
moldflow注塑cae软件是澳大利亚moldflow公司开发的,对热塑性塑料熔体进入模具的流动过程的模拟 分析 是非常成功的,特别是在复杂情况下的分析,是世界公认的注塑cae 工业 标准,它精确高效的模拟注塑工艺全过程,能使生产厂家实现高质量、低成本、短周期的目标。现在,在世界上已得到了广泛的 应用 ,有许多公司应用moldflow来改善其产品质量,缩短开发周期[2]。
对于采用普通注射成型法制造光学塑料透镜来说,由于透镜的厚度较厚,且厚度变化大,收缩系数变化大,所以很难凭经验预测模具结构和工艺参数对制品质量的 影响 。对于光学塑料零件来说,cae有更大的作用,使得能够利用普通的注塑机生产较高质量的光学塑料零件。
四、工艺参数的优化
在塑料注射成型过程中,工艺参数很多,对收缩及残余应力影响较大的主要有:注射压力、注射温度、填充速度及速度曲线类型、保压压力大小及时间、保压压力曲线类型、模具温度以及冷却系统的温度等。
由于在注射过程中过大的剪切应力会导致过大的残余应力,并可能引起塑料的分解等缺陷;又由于塑件的收缩直接影响几何尺寸和面形,所以在注射过程中的剪切应力应当控制在合理的范围内,并且尽量减小塑件的收缩。
由于浇道系统及各部位几何形状不同,不同部位对充模熔体的流动(速度、压力)提出不同的要求,否则就要影响熔体在这一部位的流变性能或高分子的结晶定向作用,以及制品的表面质量,所以这就要求采用多级注射工艺。填充速度曲线类型如图1所示。
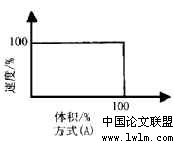
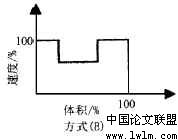
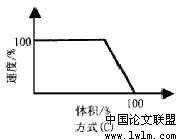
图1 填充速度曲线类型
图2是填充速度曲线类型对剪切应力的影响。
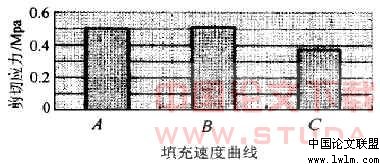
图2 填充速度曲线类型对剪切应力的影响
由图2可以看出,填充速度曲线(a)和曲线(b)的剪切应力差别极小,而填充速度曲线(c)比曲线(b)和曲线(a)的剪切应力小得多,这是因为在填充的最后阶段,边缘的厚度较薄,如果还以高的填充速度注射,必然产生较大的剪切应力。填充速度曲线(c)在注射结束阶段降低了速度,这样既可以减低剪切应力,又可以避免产生溢边的现象。所以在注射过程中,应当采用多级注射。
通过模拟分析和 理论 分析可知,填充速度越大剪切应力越大,所以填充速度不宜过大,且过大的填充速度可能引起喷射等缺陷。模具温度等参数对剪切应力的影响较小。
保压流动和充模时的压实流动都是在高压下的熔体致密流动。这时的流动特点是熔体流速很小,不起主导作用,而压力却是影响过程的主导因素。在保压阶段,模内压力和比容不断变化。产生保压流动的原因是因为型腔壁附近的熔体受冷却后收缩,熔体比容发生变化,在流入口凝固前,熔体在注射压力作用下继续向型腔补充熔体,产生保压流动。保压压力曲线类型如图3所示。
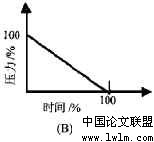
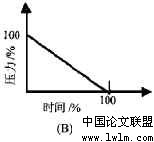
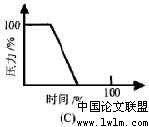
从模拟 分析 中可以得出对塑件收缩 影响 最显著的因素是:保压压力大小、保压压力曲线、保压时间,而其它因素的影响较小。收缩率随着保压压力的增大而减小。
保压压力曲线类型对塑件收缩影响如图4所示。
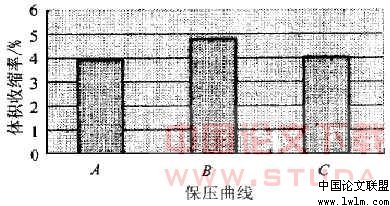
图4 保压压力曲线类型对塑件体积收缩的影响
在图4中,曲线(a)是常压方式,它不仅一直以较高的压力补充熔体,又可以使塑件在浇口凝固时产生高的“封口压力”,根据pvt方程得,封口压力越高则收缩率越小。而曲线(b)由于从开始就随时间下降,所以保压效果不如曲线(a)。曲线c的保压效果和曲线(a)相近,这种方式比较合理,因为可以使塑件在较高的压力下凝固,减小了塑件的收缩。而在浇道系统凝固后,再施加保压压力已经不能传递到型腔内,这时的保压已经没有作用,而只能使能量白白地浪费。最合理的保压方式应该选择曲线(c),既可以减少收缩,又可以避免过保压,并且能够节约能量。
根据模拟分析所选择的最佳工艺参数的剪切应力和体积收缩如图5和图6所示。
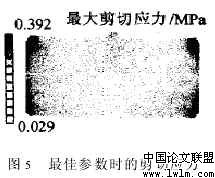
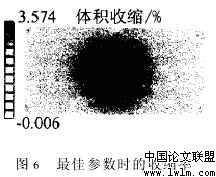
五、模具面形的补偿
模具面形补偿有两种 方法 :成型后测量变形的补偿方法和成型前预测变形的补偿方法[3~4]。
目前 普遍采用的模具面形补偿方法是成型后测量变形的补偿方法,这一方法中的评价技术、补偿技术以及连续成型的稳定性是决定性因素,其过程如下:用形状和设计值接近的模具进行实际的成型,评价在最合适的工艺条件下成型的模压零件,并与模具形状相比较, 计算 模具的补偿量,修正模具面形,再进行成型,直到成型的零件合格为止。
对于透镜来说,形状误差不仅仅是由于树脂收缩而造成的,弯曲和脱模时的变形也起重要的作用。由于塑料的成型是一个复杂的过程,成型品各个部位的变形及收缩是不同的,随成型品的形状和工艺条件的变化而不同。这就决定了补偿过程是一个费用高、时间长的反复过程。
另一种对模具面形的补偿 方法 是成型前预测变形的补偿方法,它是根据cae软件对复杂的零件模拟 分析 ,不用制造模具就可以确定零件各部位的收缩率及变形,然后修改模具面形的几何尺寸,再进行模拟分析,使得可以加工出满足要求的零件形状。这种方法节约了模具的制造试制费用,缩短模具开发时间,提高了塑件成型的精度。
因为在模具加工完后进行试模,模具可能不完全合适,还需要修模,所以在一般模具制造中,把型腔做的稍微小一些,以便在修模的过程中模具可以直接在模具上加工,否则如果模具型腔太大,则需要对模具进行补焊或镀膜,这将大大增加加工的难度和成本。
在进行模具面形补偿时,为了便于模具的修模,补偿的面形应当使模具的型腔也小一些,即模具型腔保持最大的实体,如图7所示。在图7中,曲面a为补偿后的模具面形,曲面b为根据 计算 机模拟分析的结果或所要求的模具面形,用此模具面形在设定的工艺条件下可以产生所设计的透镜形状。但是由于直接加工曲面b是不可能的,所以要用可加工的曲面来近似,这可以选用球面或回转非球面。所以在曲面拟合时使负误差比正误差小,使负误差与正误差的比值为一个小数,用此条件作为优化函数的约束条件。在此约束条件下使补偿的面形与模拟分析所要求的面形的误差加权平方和最小,求得此时的面形参数,这样就有利于模具的修复。
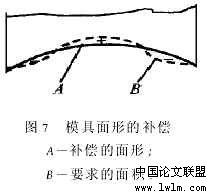
光学透镜的面形是对称旋转曲面,为了便于加工,模具的面形选用旋转曲面。高精度的型腔面形可以采用单点金刚石加工的方法,它的加工精度很高,可以直接加工出高精度非球面的面形。设模具补偿的面形方程为z=φ(x,y)。如果根据计算机模拟的结果计算的理想模具面形为z=φ(x,y),则补偿曲面与理想模具面形的误差为δz=φ(x,y)-φ(x,y)。
根据最大实体原则得到
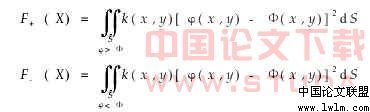
其目标函数为
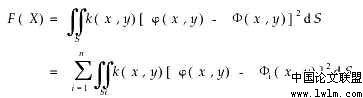
约束条件为f-(x)=ηf+(x),η为一个正小数,即h(x)=ηf+(x)-f-(x)=0
利用罚函数法求函数f(x)的最优解x ,就得到了模具面形曲面方程的参数。根据以上的目标函数和优化方法,可以求得模具面形,使它成型出的零件最终尺寸接近零件面形几何尺寸的要求[5]。
六、结论
本文介绍了利用先进的塑料模拟分析软件moldflow对光学塑料透镜进行了模拟分,可以对各种工艺参数进行优化以取得最佳的成型结果。采用优化技术等计算方法在成型前对其进行了模具型腔的面型补偿。采用成型前补偿模具的方法可以大大减少模具的试模和修模次数,能够提高成型的面型精度,这将减少开发费用、开发时间,并提高了制品的质量。