阐述了基于汽车覆盖件板成形的有限元模型 分析 软件autoform的模具cae技术,对其特点和功能作了阐述。以风神bluebird发动机罩外板的模具调试为例阐述了其实际 应用 ,对拉延模的模面设计方案进行了分析,对其拉延成形过程进行了模拟分析,并依此对拉延模的调试方案进行分析和判断,优化了改进方案,和现场取得了完全一致的结果。
一、前言
当代汽车和 现代 模具设计制造技术都表明。汽车覆盖件模具的设计制造离不开有效的板成形模拟软件。国外大的汽车集团,其车身开发与模具制造都要借助于一种或几种板成形模拟软件来提高其成功率和确保模具制造周期。
作者从2001年5月开始探讨autoform在解决汽车覆盖件模具制造中的应用,经过各个阶段的重点攻关,实现了:对汽车冲压零件产品的可冲压成形性进行分析,判定成形的难点和关键区域;对汽车冲压零件产品实现毛坯展开 计算 ;对模具和工艺方案的确认进行有选择性和针对性的模拟分析,给模具调试提供量化的分析判断数据,对可进行的模具调试方案进行判别,并对可行的调试方案提供具体技术参数;对模具和工艺方案进行反复优化的多次模拟,用先于现场模具调试的模具cae技术,对拉延模具设计的可行性和可靠性进行量化的分析和判断,对有欠缺的设计提出优化改进方案:
二、autoform的功能和特点
autoform提供了从产品的概念设计直至最后的模具设计的一个完整的解决方案,特别适合于复杂的深拉延和拉伸成形模的设计、冲压工艺和模面设计的验证、成形参数的优化、材料与润滑剂消耗的最小化、新板料(如拼焊板、复合板)的评估和优化。www.11665.com
从数据输人到后处理结果的输出,autoform融合了一个有效开发环境所需的所有模块,从前处理到后处理的全过程与cad数据的自动集成,网格的自适应划分,所有的技术工艺参数设置的过程易于理解且符合工程实际。
autoform使用了许多现代模拟技术:应用新的隐式有限元算法保证求解的迭代收敛;采用自适应网格、时阶控制、复杂工具描述的强有力接触算法、数值控制参数的自动决定和使用精确的全量拉格朗日 理论 等保证求解快而且准确。它同时融人了许多工程应用技术,如考虑了加工硬化和应变率效应的各向异性材料模型;等效拉延筋阻力模型。
autoform对模拟结果融合了许多有效的解释:可以实时地观测计算结果;可观测应力、应变和厚度分布、材料流动状况;可计算工具应力、冲压力;可实现材料标记、法向位移的标识;可生成对破裂、起皱和回弹失效进行判定的成形质量图以及成形极限图;还可进行动画显示和截面分析等。
三、模面设计
在风神bluebird发动机罩总成模具的设计与制造工作中,为保证模具的制造质量和周期,作者对其主要零件-发动机罩内外板进行了成形模拟分析,取得了良好的应用效果。以下主要对外板作一个说明。
1、产品介绍
发动机罩外板如图1所示。料厚:0.8(gb708-88)。材料:sp780-340。坯料尺寸:0.8*1540*1770。其冲压工艺是:开卷落料,外形定位拉延成形,外形与形状定位修边冲孔、吊楔修边,外形与形状定位翻边、吊楔翻边,检验夹具。
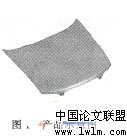
2、拉延成形模面设计
模面设计是根据冲压工艺和模具设计知识,完成优选冲压方向、压料面形状的确定、工艺补充面的设计以及拉延筋的设计与布置等,依其掌握的经验和知识,以获得最佳的材料流动,达到拉延出合格的拉延件的目的。
(1)冲压方向的确定.在保证没有冲压负角的情形下遵循平均法向原则、最小拉延深度原则、无冲压负角原则、确定冲压方向:绕坐标轴z旋转+15。,如图2所示。
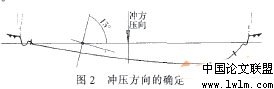
(2)压料面的设计.首先遵循平顺光滑原则,在具体设计策略上重点考虑拉延深度、压料面截面线轮廓的处理,压料面面轮廓的处理,压料面的位置确定。
(3)工艺补充面的设计.首先应考虑到后续工序(如修边、翻边)的衔接和模具结构上实施的可行性与简便性,然后就是考虑材料的局部流动情况及其对拉延成形的 影响 。工艺补充面的设计有2个重要的参数,即凸模圆角半径和凹模圆角半径的设计。
(4)拉延筋的设计与布置拉延筋在调节局部进料阻力上有着非常直接的作用,在布置时还要考虑到后序修边和拉延时很可能产生的拉毛 问题 。在模面设计进行时,对类似零件的模面设计及其实际冲压情况进行了调研,力求让外板有充分的变形、良好的刚性;同时探讨使用板成形数值模拟技术对数据量大、使用新材料的发动机罩内外板进行冲压模拟 分析 ,对现场模具调试出现的问题进行分析判断,并协助解决现场出现的调试问题。
四、成形模拟分析
1、有限元网格模型的建立
通过标准的iges数据转换接口,将工具和坯料的几何模型读人有限元分析系统中进行网格划分,对覆盖件成形模拟分析可用bt壳单元对几何模型进行离散,建立零件的有限元网格模型,由于采用真实拉延筋和工艺补充面形状复杂,有限元网格模型的节点数和单元数很大,其节点数为118778,单元数为127778。并进而建立一个模具的有限元 网络 模型的装配,如图3所示。
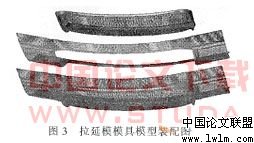
这是一个典型的双动拉延模,板坯首先放在凹模上并定好位置,板料在重力作用下会有一定的下垂,即重力效应;然后压料圈在压力机外滑块作用下下行完成压边成形过程,接着凸模在压力机内滑块作用下下行完成拉延成形过程。
2、板坯及其材料性能参数
关于毛坏形状,应优先采用方形或方形切角,这样可以减掉落料模具;然后是有一定规则形状的毛坯,这样既可简化落料模具结构,又给优化毛坯排样提高材料利用率提供了良好的基础;最后是任意形状的毛坯。 目前 也有考虑套裁和组合成形技术,并有成功 应用 实例。
在数值模拟分析的前处理中,对板坯进行网格划分,板坯外形尺寸为1550*1770,考虑到制件左右对称,在定义好对称面后只需对其一半进行求解 计算 。虽然板坯初始网格单元数为1736,同样由于采用真实拉延筋和工艺补充面形状复杂,尤其是小的圆角,所以基于自适应精化网格技术的autoform自动根据板料变形情况进行网格重划分,到拉延结束时板料网格自适应精化级别达到5级,所需单元数达到1759014,实用单元数达到1777644。
材料的性能参数:屈服强度σs=162.86mpa;抗拉强度σb=315.35mpa;延伸率δ=47.17%;强度系数k=556.08mpa;硬化指数n= 0.227;0°、45°、90°力一向上的厚向异性指数:分别是1.774、1.842,1.941。
3、拉延成形模拟分析和拉延模的调试
(1)第1阶段的模拟分析
采用非方形毛坯,通过调节压料力和摩擦系数等冲压成形工艺条件和参数,经过多次模拟分析直至得到此条件下的最佳拉延成形效果的板料毛坯和成形参数,结果如图4所示。可以看出:a区破裂,b区接近破裂,c区变形刚性不足。

(2)第2阶段的模拟 分析
为消除c处变形刚性不足,在后侧毛坯采用直线形状,经过模拟分析其结果如图5所示。
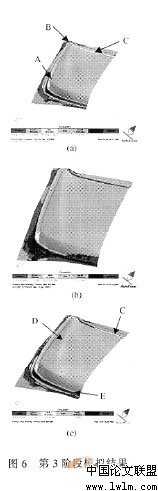
可以看出,由于毛坯形状的变化和压料力的降低,a区破裂有所缓解,召区情况未变,c区由变形刚性不足到由于材料流动困难而破裂:但破裂区域在修边线以外,而且修边线以内的有效区域得到了充分良好的变形,后一点正是所希望的。
(3)第3阶段的模拟分析
在第2阶段模拟结果的基础上,进一步尝试采用规则的方形毛坯,这样就不需要落料模。经过模拟分析其结果如图6(a)所示。结论:采用规则方形毛坏是可行的,前提是消除a,b,c处的破裂。
减少压料力和降低模具表而摩擦,虽能消除破裂,但制件变形很不充分局部甚至起皱,如图6(b)。大多数处于两种情形之间,如图6(c)。
从上述模拟分析情况也可以同时得出以下结论。
(1)c区是最易破裂部位,其次是.4区、b区;若采用减少压料力等则c区仍破裂,a区、b区破裂消失,d区成为变形不足的部位,d区变形不足甚至局部起皱。
(2)必须进一步采取一些修模措施,改变材料的流动情况,使c;区的材料加快流动,使d,e区的材料减缓流动,达到材料均匀流动和变形充分、均匀的目的。
五、现场调试
根据上述拉延成形模拟分析的结果,可以很容易地找到模具调试方案。
如图7所示,由于沿周工艺补充面拉延包过高,并且r太小,使材料流人困难,过高的筋同时也意味着材料的局部剧烈形状变化,导致在拉应力作用下失稳破裂。现场实冲结果如图8所示。
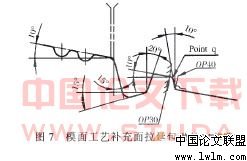
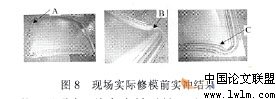
按上述分析,首先降低压料面及凹凸模具表面粗糙度,用砂轮机修整以降低沿周拉延包的高度,同时适当放大破裂区域部位的凹模圆角半径,以便于材料的流动,消除破裂。现场最终的实际调试结果是:c区拉延包高度最大处降低约15mm,两侧及角都降低约5mm;为了消除b区仍存在的局部材料过度变薄和微小裂纹,将角部凹模r由r5修磨到r10,彻底消除了微裂纹。
模具经上述实际调试后结合cae提供的冲压工艺参数进行试冲的结果如图9所示,得到了完全合格的拉延件。
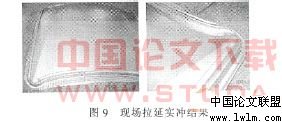
从上述过程可以看出,采用数值模拟技术来进寸拉延成形分析,并进而在模具制造调试时提供量的数据和判据,指导模具调试,这是缩短制模周期、提冲压件成形质量的一个非常重要的手段。若在模具加工制造前就进行充分的模拟分析,研讨模面设计的可行性和可靠性,并进而提出改模方案,更改nc加工代码,无疑将大大减少现场实际试模量,该技术的成功 应用 也预示着其巨大潜力。但板料的冲压成形过程和模具的设计制造是一个十分复杂的系统过程,单对某一个工序及其模具调试作出分析、判断和成功的修改或完善还是不够的,还需对许多关键技术作进一步的 研究 和探索,才能最终大大减少现场模具调试的工作量。